Bridging the Gap Between Video Games and Real-World Robotics
3 min read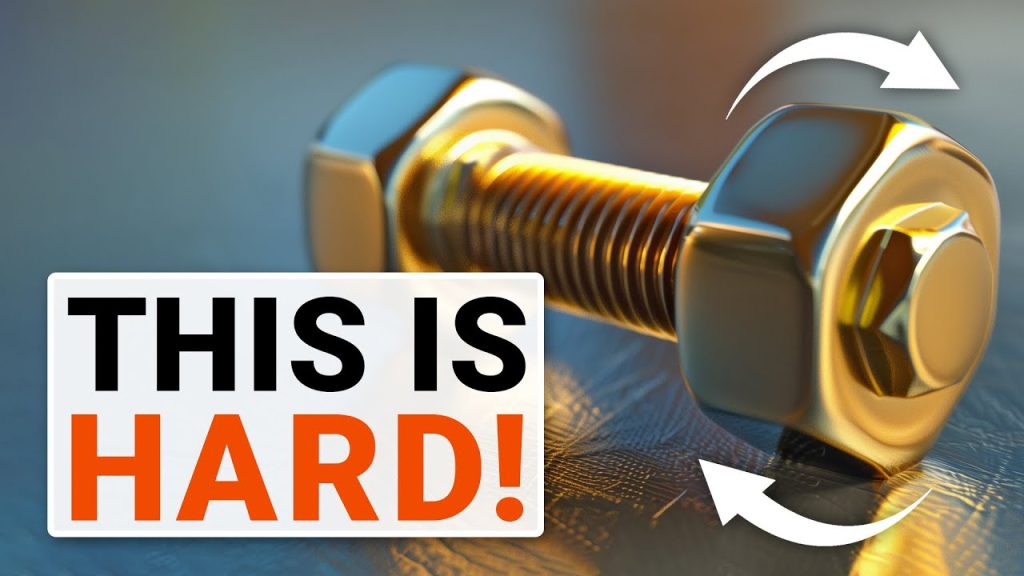
In a fascinating blend of video games, reality, and robotic technology, researchers explore how these elements can come together to revolutionize manufacturing. Factories already use specialized robots for efficient production, but these robots are costly and rigid in their functionality. Therefore, a recent study dives into how general-purpose robot arms, which are more affordable but currently unreliable and slow, can be trained using simulation techniques borrowed from video games. This method aims to bring the virtual world’s flexibility and speed to real-world applications. However, significant technical challenges must be overcome.
Robotic Advancements in Factories
Factories have long relied on robotic contraptions to build items cheaply and efficiently. These specialized robots excel at their tasks, but there’s a catch—they’re expensive and tailored to specific jobs.
General-Purpose Robot Arms
A recent research paper introduces a more cost-effective alternative: general-purpose robot arms. These robots are cheaper but come with their own set of issues, such as being unreliable and slow.
Training Robots in Simulation
The proposed solution involves training these robots in simulation, letting them practice assembling objects in a virtual environment before doing it in real life. However, simulating even basic tasks like screwing in a bolt demands a high level of geometric accuracy, making it computationally expensive.
In practical terms, simulating a single bolt might require around 50,000 elements colliding with each other. This complexity often makes the simulation look nothing like reality.
Challenges in Geometry Representation
Even representing the geometry of a simple bolt poses a challenge. Although convex decomposition and triangle meshes offer some solutions, they are not perfect and can be computationally expensive.
Collision detection between nuts and bolts takes too long, posing a significant hurdle for real-time applications.
Luckily, a new paper proposes a method to represent these geometries in a detailed way, and the nut and bolt simulation runs in real-time successfully. But, the limitations in computational and memory resources mean that only about 20 nuts and bolts can be simulated simultaneously.
Speeding Up Simulations
The computation of interactions between 16,000 contact points is a major bottleneck. Remarkably, the recent research offers a solution to reduce these points by 98%, bringing them down to around 300.
This improvement allows tens of thousands of nut and bolt interactions per second, making large-scale simulations possible. The simulation is not limited to nuts and bolts but can handle other objects effectively.
Furthermore, this system can run more than 100 environments in parallel, paving the way for full assembly boards of commonly used parts to be simulated down to the last millimeter. For example, even a virtual USB-A adapter can be plugged in with high accuracy.
Teaching Robots to Use Objects
The next challenge is teaching robots to handle these objects correctly. Thanks to the proposed methods, after an hour and a half of training, robots can achieve a success rate of over 85% when picking up and screwing in a nut.
Even in the worst scenarios, the success rate remains around 75%, making it a reliable solution. Compared to humans, these robots apply a narrower range of force, offering a consistent and efficient method.
This remarkable success brings us closer to solving a problem once thought impossible, achieving these results 10,000 times faster than previous techniques and allowing multiple factories to run on a single graphics card.
In conclusion, the integration of video game techniques in training general-purpose robot arms marks a groundbreaking advancement in manufacturing.
By overcoming significant challenges in simulation accuracy and geometric representation, researchers have made it feasible to simulate and train robots in complex tasks efficiently.
This innovation not only accelerates the training process but also ensures high success rates, bringing us closer to a future where affordable and versatile robots can revolutionize factories.